こんにちは!あるぱかです。ロボットハンドの設計についてメモします。
ロボットハンドの設計は、ロボットシステム全体のパフォーマンスを左右する重要な要素であり、設計者の腕の見せ所です。そのため、設計ミスを避けることが重要になります。
最も避けたいことは、ロボットハンドが重すぎて本来の性能を引き出せなかったり、異常や故障が発生することです。 例えば、
・ハンドが重すぎて加減速を落とさざるをえず、タクトタイムが伸びた
・各軸に過負荷がかかり、エラー発生で動かせなくなった
・部品が短期で故障し、交換が必要になった
これらは本来、設計段階で解消できるはずですが、設計者が「多少重くても問題ないだろう」と油断し、実機調整段階で発覚することもあります。
目指すべきは
・ロボットにかかる負荷を最小限に抑え、速いスピードで作業させる
・機構部品の故障を防ぎ、寿命を長くする
この記事では、重量情報の観点からロボットハンドを設計する上で知っておきたいポイントをまとめます。
【設計の基礎知識】
可搬重量の定義
可搬重量(Payload Capacity)とは、ロボットが安全に持ち上げ、移動できる最大重量のことです。
ロボットハンド総重量 = エンドエフェクタ重量 + ワーク重量+α
(α:ケーブルの配線類など、3D CADでは再現しきれない要素)
重要な注意点として、『可搬重量=そのままの重量を持ち上げられる』という単純な意味ではないことを理解しておきましょう。
「可搬重量」の意味は、重心がフランジ面上にあるときの最大重量を示します。重心がフランジ面から離れると、ロボットの各関節にかかる各関節にかかるモーメント(トルク)が増加し、実際に持ち上げられる重量は減少します。
例えば、可搬重量10kgのロボットでも、実際には7kgが限界ということもあり得ます。
各ロボットメーカが提供する可搬重量ー重心位置の曲線グラフを確認し、適切な設計を進めてください。
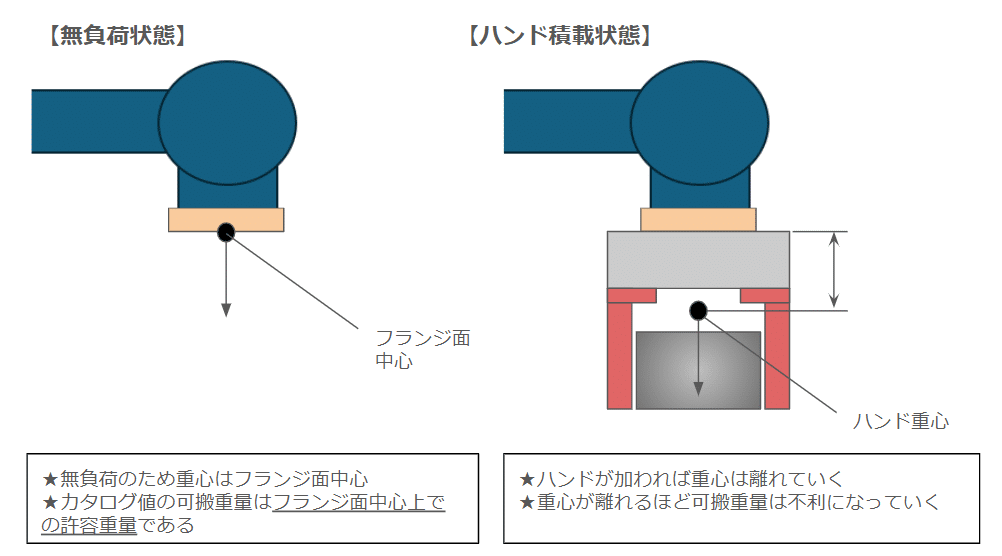
限界取付寸法
各メーカーの取り扱い説明書には、可搬重量ー重心位置の曲線グラフ「限界取付寸法」が記載されています。(具体的なメーカ:FANUC、安川電機、KUKA、、)
まず3D-CAD上でハンドの重量と重心位置(A,B)を求め、該当する取付寸法表のグラフにプロットし、適正範囲内にあるかを確認します。※下図参考
必要な情報
ロボット5軸回転中心から見たハンドの負荷重心位置 A,B寸法:
P点と呼ばれる5軸目の中心からの距離を示します。フランジ中心からの距離と勘違いしやすいので注意。P点位置は各メーカの外形寸法図を参照してください。
ハンド重量:
上述した式「ロボットハンド総重量 = エンドエフェクタ重量 + ワーク重量+α 」で算出します。3DCADで算出しますが、各パーツ、購入品の材料設定や質量設定を間違いなく整えた上で、実物に近い状態にしましょう。
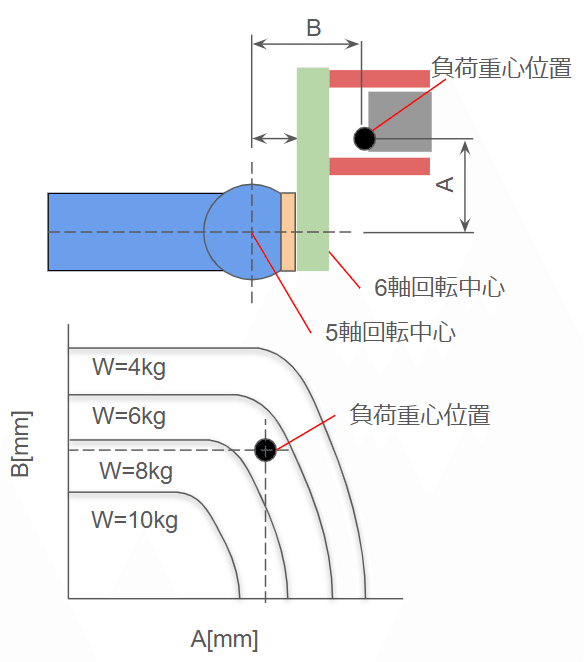
許容範囲内に入っていれば問題ありませんが、だからといってあまりにもギリギリな設計は避けたいところです。ある程度の余裕度は見た方がいいでしょう。
許容オーバーしたときのロボット動作
許容範囲を超えると、ロボットに過負荷がかかり、減速機の摩耗が進み、交換頻度が増えるリスクが高まります。
許容値を超えた場合、ロボットの制御ソフトウェアが自動で加減速を落とす方向に調整することがあります。(※ただし、メーカーによっては警告を出して動作停止する場合もあります)
このように速度リミットを設けることで負荷を軽減することはできますが、一定以上の過負荷がかかるとエラー停止します。
速度減少や停止すれば、サイクルタイムが伸び、生産ライン全体への悪影響に波及します。そうならないためにも、やはり設計段階での対策が必要になってきます。
【許容オーバーしたときの対応策】
オーバーしたときどのように対策を進めればいいでしょうか?以下3つ方法があると考えています。
対策①ロボット変更
例えば、「25kgタイプでは足りないなら、35kg可搬のロボットに変更しよう」と考えるかもしれません。ただし、注文後に問題が発覚すると変更は難しくなります。特に、
- 設計段階での客先からの仕様追加(ハンドチェンジャ追加など)
- ワーク品種追加改造による重量アップ
といったケースでは、ロボット変更が現実的でない場合が多く、ハンド設計の見直しが求められます。ロボット変更ができる段階であっても、当然金額も必要スペースもアップします。ですので、改善の余地があるのなら、安易にグレードを上げず、設計変更で最適化するのがベターです。
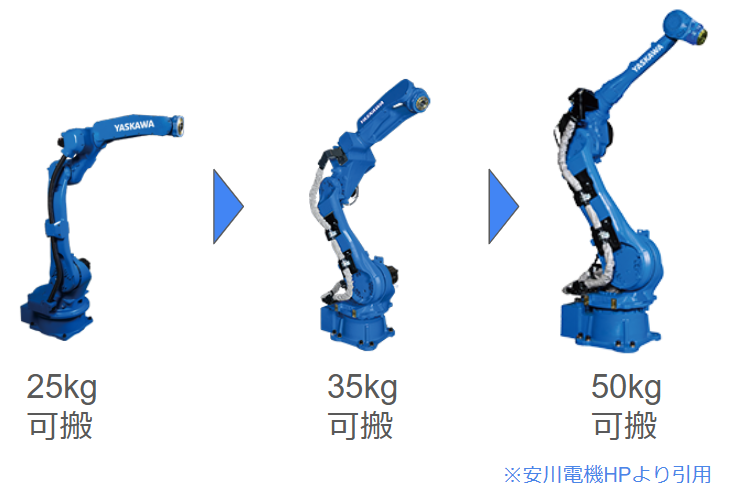
対策②ハンド軽量化の設計
ロボットハンドの軽量化には、材料変更と設計の最適化の両面からアプローチすることが重要です。
1. 材料変更
- アルミニウム合金A2017(ジュラルミン)
- SS400の1/3の重量で、十分な強度と剛性を持つ
- CFRP製の「フェルカーボ」(双葉電子工業)
- アルミの1/2の重量で、1.3倍の剛性を持つ(高価)
ただし、CFRPは加工性に制約があり、コストも高いため、実際の用途に応じた選定が必要です。
新材料フェルカーボ | 双葉電子工業 | 日本 双葉電子工業では軽量で加工性の高い新材料フェルカーボの開発に成功しました。CFRPをベースにした厚板でアルミなどからの置き www.cfrp.mtb.futaba.co.jp
2. 設計の最適化
材料の変更だけでなく、構造自体の見直しを行うことでさらなる軽量化が可能です。
- トポロジー最適化(形状最適化)
- 必要な剛性を維持しながら不要な部分を削減し、軽量化を図る
- FEM解析を活用し、応力分布に基づいて最適な形状を設計
- リブ構造の採用
- 板厚を減らしつつ、リブを追加して剛性を確保
- 一般的に、リブを入れることで重量を30%削減できるケースもある
- 参考:板金部品の剛性アップ設計。制約があっても諦めない
- 部品点数の削減・一体化設計
- ボルトや補強プレートを減らし、一体成形や溶接構造を活用することで重量を削減
これらの工夫を組み合わせることで、軽量化と剛性確保のバランスを取りながら、ロボットハンドの設計を最適化できます。
対策③重心の移動
重心をフランジ面に近づけることで、許容範囲内に収めることが可能です。
- 基部(フランジ近く)に重い部品を配置(アクチュエータ、センサ類)
- 手先部(ワーク近く)に軽量部品を配置(搬送用途なら爪のみ)
重心移動の考え方として、アクチュエータを基部に配置する方法が有効ですが、ワークの形状によっては適用が難しい場合もあるため、バランスを考慮する必要があります。
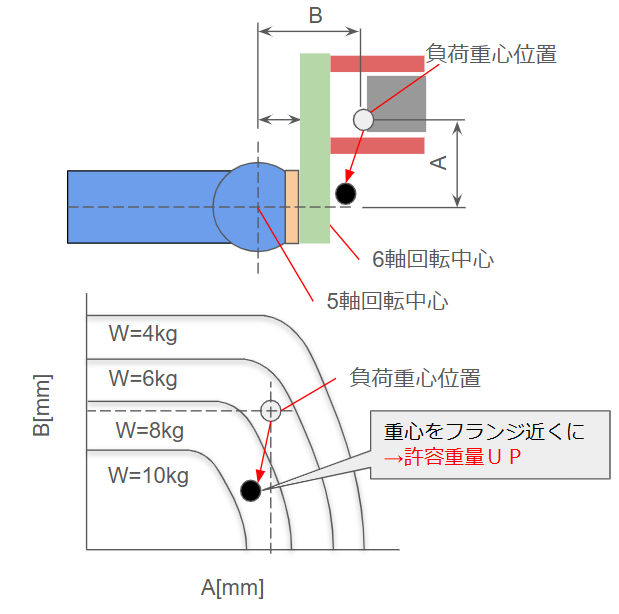
まとめ
本記事では、ロボットハンド設計で押さえておきたいポイントをまとめました。 特に、可搬重量の考え方や限界取付寸法の確認方法を紹介し、質量情報(重量・重心)の重要性を解説しました。
これらの知識は設計段階で見落とされがちなので、十分理解して活用してください。
ご不明点やご意見があれば、ブログのコメント欄またはX(旧Twitter)までDMをお寄せください。Xアカウント:@AlpacaRobotics